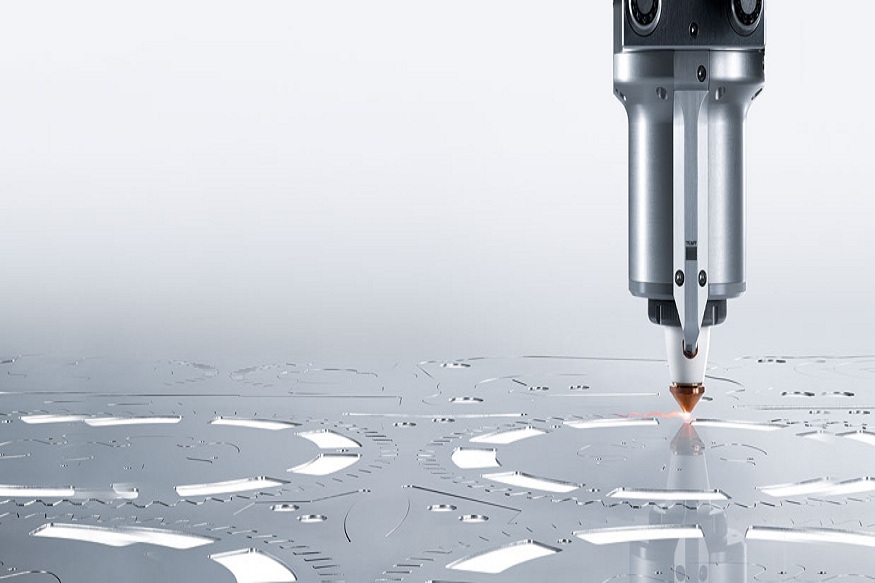
Choosing the right machinery servicing supplier can significantly either build or bring down your company within the current highly competitive world economy of today. It can therefore be said that industrial machinery services affect your production, down time and profit regardless of the size of your manufacturing plant. In the case of selecting industrial machinery services, the present thorough guide will assist you in making the right decision by giving you five important tips.
1. Experience and Technical Expertise
Experience and technical know-how are the foundation of any trustworthy machinery service provider. Seek out service providers who have experience working with equipment like yours. In addition to knowing the nuances of various machinery kinds, a team with a lot of expertise will also know how to solve typical problems. This knowledge frequently results in more precise diagnosis and quicker issue solving.
The credentials and certificates of the service team justify relative judgments about technical skills more adequately during skills assessment. Accreditation from widely recognized professional bodies demonstrates an assurance to abide by high standards besides keeping abreast with the new technologies. Also, professional service providers tend to keep in touch with OEMs so as to get original parts and the latest details from them.
Think about the variety of equipment the service provider has used in your sector. A wide range of experience points to flexibility and thorough understanding, which are crucial for handling complicated equipment problems. Through case studies, customer endorsements, and thorough justifications of their methods for resolving issues, the top service providers will be able to showcase their proficiency.
2. Response Time and Availability
Time is literally money in the industrial sector. Production losses can be substantial for every minute of outage. As a result, while choosing a machinery service provider, you should give careful consideration to their availability and response time. The top service providers are aware of this crucial factor and make explicit promises about how quickly they will respond to certain service requests.
Seek out service providers with a clear system for allocating service calls and round-the-clock emergency assistance. They must be able to give you several ways to get in touch with them as well as a transparent escalation procedure for pressing issues. The service provider’s capacity to react promptly to your needs is also greatly influenced by their geographic location and coverage region. It’s good to look into whether they have service centers or mobile units positioned in close proximity to your establishment.
To reduce unplanned malfunctions, a trustworthy service provider should also give preventive maintenance plans. They should take a proactive stance, giving flexible service hours to meet your operating demands and recommending maintenance windows that coincide with your production schedules. Your choice should also take into account the provider’s capacity to maintain steady availability during holidays and busy times of the year.
3. Equipment and Resources
Service of modern industrial machinery necessitates specialist equipment and advanced diagnostic tools. A service provider’s capacity to provide efficient solutions can be strongly impacted by the caliber and variety of tools and resources available to them. To guarantee they can manage a range of maintenance and repair issues, top-tier service providers make investments in the newest diagnostic technology, specialist tools, and state-of-the-art facilities.
Think about the provider’s expenditure on technical resources like repair guides, diagnostic software, and access to manufacturer support networks in addition to physical tools. Their dedication to offering complete service solutions is evidenced by this infrastructure. Examine their parts availability and inventory management system as well. The finest service providers frequently keep common replacement parts in stock and develop partnerships with trustworthy parts suppliers.
Human capital is equally vital. A team of experts with a variety of skill sets should be employed by the supplier to handle a range of machinery and issues. For business employees to stay up to date with changing maintenance methods and technology, they need also regularly fund training and skill development initiatives. For seamless service delivery, a robust support team, including project managers and customer service agents, is necessary.
4. Safety Standards and Compliance
Safety is crucial in industrial environments. Your choice of machinery servicing provider needs to show a strong dedication to safety regulations and legal compliance. This entails keeping the right credentials for their technicians and operations, adhering to industry-specific safety procedures, and having adequate insurance coverage.
Seek out providers who can show you their safety records and who have a written safety program. They should enforce stringent safety regulations during all servicing operations and supply their technicians with the appropriate personal protective equipment (PPE). The top suppliers will also be knowledgeable about the rules and guidelines that apply to your sector, such as OSHA regulations and particular safety precautions for your kind of equipment.
An essential component of their service approach ought to be risk assessment and management. They ought to be able to recognize any risks, put suitable safety precautions in place, and keep track of all safety-related processes. Take into account their history of workplace incidents as well as how they handle staff safety updates and training. A supplier that puts safety first will assist safeguard your workers and your equipment.
5.Quality Assurance and Documentation
The service provider’s approach to documentation and quality assurance is the last important factor to take into account. All maintenance and repair work, including inspection reports, service history, and repair documentation, are meticulously documented by reputable service providers. Maintaining warranty coverage, scheduling maintenance, and monitoring equipment performance all benefit from this documentation.
Clear processes for testing and confirming repairs, as well as procedures for managing complaints and customer feedback, are essential components of a strong quality assurance system. The supplier must be prepared to back up their work with suitable guarantees or warranties. Additionally, they must have mechanisms in place for tracking and evaluating the quality of their services, such as frequent performance evaluations and polls of client satisfaction.
Detailed service reports, maintenance suggestions, and cost projections should all be included in documentation procedures. The top suppliers will give you thorough, easy-to-read reports that will assist you comprehend the work done and decide what maintenance is necessary in the future. Additionally, they must be able to offer this data in a way that works with your maintenance management programs.
Conclusion
When choosing an Advanced Machinery Solutions in saudi arabia, there are a number of aspects to carefully examine. By assessing possible suppliers according to their resources, safety standards, experience, reaction time, and quality assurance procedures, you can make an informed choice that will ultimately improve your business.